Carbon
- "Soot" - part of combustion
The
more modern the engine, the bigger the carbon issue. This is -with
lubricity - the biggest reason to utilize our fuel catalyst. It
is an undisputed fact that we lower carbon during the combustion
process due to improved combustion and increased lubricity that
extends injector efficiency on spray patterns. The fact that we
save small amounts of fuel 5-7% is a purely financial short-term
bonus. The long-term effect is that we extend economical engine
life and lower the possibility of costly engine failures that has
a huge cost impact and negatively impacts on asset utilization.
Build
up of carbon on fuel injectors causes poor spray patterns, resulting
in less effective burning of fuel. This affects every element around
the combustion chamber, increasing heat, oil dilution, emissions,
fuel consumption and shortening the engine life cycle. Carbon penetrates
everywhere and is highly abrasive by nature.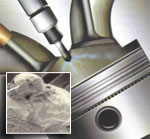
Due to stop / start driving in cities, extended
idling and worsening traffic congestion, the engines are building
up vast amounts of carbon everywhere from the injector tips to valves,
EGR, turbo's, filters, exhaust system etc.
Flameproof equipment suffers from carbon buildup.
We reduce the carbon visibly and extend the efficiency due to extending
carbon blockage intervals. This effectively improves the combustion
process with lower emissions and raises asset utilization due to
extending cleaning intervals.
The product reduces carbon build-up in engines
as a result of improved fuel combustion in the engine chamber, reducing
abrasive engine wear and extending engine oil integrity due to less
soot and fuel dilution.
Materially less carbon during
combustion process. Carbon is highly abrasive and affects spray
patterns and valves
Carbon is a major growing problem in South Africa and will soon
rival lubricity, as we enter the Euro 3 to 5 technology phase.
There are a number of reasons, all working collectively to exacerbate
soot formation:
- 30% more aromatics per volume in South African than the European
EN 590 fuel standard
- South African fuel contains more lower end carbon chains which
affects the burning process
- High altitudes above sea level coupled with dry climate
- Poor air filtration that reduce air quality
- Undulating terrain
- Higher payloads -Superlink
- Traffic congestion
- Maintenance
- Inadequate driver training
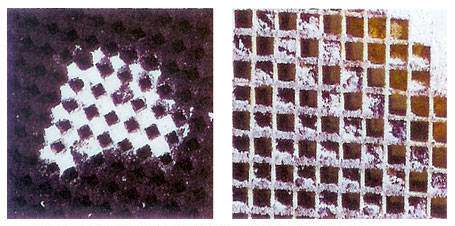
Diesel particulate filters clogged with particulate matter
Soot is 20x smaller 20 xs more abrasive than silica
Fuel injector system and engine designed
specifically for EN 590 (European Fuel spec) compliant fuel?
Material
difference in Aromatic levels (up to 36% of total diesel volume).
SA aromatics 42% max of volume in 2006 SANS 342:2005
Future dates 35% max of volume?
(Government Gazette 12 Dec 2005)
European EN 590 11 % max of volume in 1999
European EN 590 6 % max of volume currently
Note: material difference between number of carbon molecules and
nature of carbon bonds between aromatics and paraffins.
Diesel Compositions: (9-23
C-atoms) |
Paraffin’s (straight-chain
HC's) |
 |
Naphthenes (cyclic HC's) |
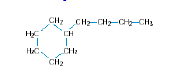 |
Aromatic compounds (benzene
rings) |
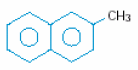 |
|
Fact on SA Fuels even after the "new diesel". SANS 242:2005
Large percentage of SA diesel does not pass EN 590 distillation
test curve
This affects fundamentals of fuel during the fuel injection and
combustion process
This directly impacts on the efficiency and life cycles of modern
engines and the many millions spent on developing engines that are
economically and environmentally friendly. This phenomenon affects
all modern engines across the world
The misalignment of fundamental fuel characteristics is a costly
exercise

|