iFleet Automated pressure & coalesce water separator /filtration
Benefits:
- Highly effective way of water removal at a flow rate of 150 litre per minute
- Water is drained automatically with iFleet technology and no operator intervention is required
- Remove large contamination particals
- Eliminate monthly cartridge replacements
Ideal for most small bousers with flow rates lower than 150 litres per minute
Allows effective upstream removal of water contamination before entering a vehicle’s fuel tank.
No monthly replacement of cartridges resulting in materially lower monthly operational costs
Highly effective at any sample interval, during and throughout operation
Fully automated water drop into separate flameproof container.
Handles bouser flow rates up to 150 litres per minute. If the 150 litres per minute is exceeded then the filters are fitted in a parallel configuration.
Not a water -wax based absorption media whose efficiency deteriorates as it reaches saturation or is diversely affected by dirt contamination and then has a direct drop in efficiency
Applications
- Main fuel bouser water separation /filtration - if flow rate higher than 150 litre –fit two units in parallel
- Ideal for kidney systems as utilised in– iFleet fuel kidney recirculating filtration systems for fuel bowsers and
genset
- There is a full range of smaller units for onboard vehicles /equipment available that caters for all flow rates
Why effective upstream water separation/ filtration?
The same principles as particle contamination - read more
Diesel is hydroscopic and when it leaves the refinery water is already present.It is a magnet for water throughout its existence. Inadequate storage facilities and neglected housekeeping increases your total costs exponentially as you migrate to new technology.
ADE engines could run with as high as 8 % water suspended in the fuel for short distances, thus virtually turning into “a steam train”, as they only had injector pressures of 170 bar with huge clearances. That is why most “snake oil” fuel additives have large quantities of emulsifiers or surfactants and thus should be avoided.
In all common rail engines all contamination – both particle and water -is fatal to their performance or failure. Minute free water droplets are problematic. Therefore it could be costly to only rely on the onboard water filters to cope with all volumes of water contamination, as water levels directly impact on efficiency, and they all have capacity constraints.
What does free water do?
Water lowers lubricity in Fuel
Promotes bacterial growth & Algae infestation
Exacerbates fuel tank corrosion and leads to subsequent metal particle contamination
Directly negatively effects the fuel burn during the combustion process
Turns to steam during combustion, which creates huge pressure (pop rings)
Avoid additives that are emulsifiers or surfactant based - it can be costly
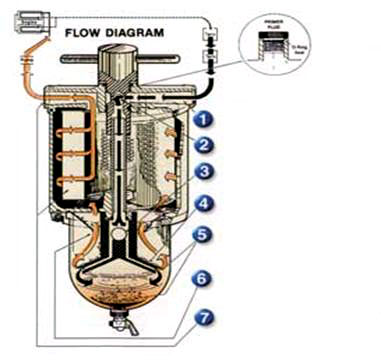
How it works
- Contaminated fuel enters the inlet port.
- The fuel is directed down through the center tube.
- Fuel flows through the reverse flow valve.
- As fuel is discharged from the depressurizer cone, 80 percent of the contaminants are separated from the fuel. Fuel rises upward and most of the solid contaminants and water settles into the bowl's quiet zone.
- As the fuel rises upward, any remaining small water droplets collect on the depressurizer cone, baffle and bowl surfaces. The size and weight of the droplets gradually increase causing the droplets to flow downward into the sump.
- Water is drained automatically from the bottom sump. This ensures that the filter remains optimally efficient at all times.
- Fuel returning restriction free, without free water contamination
|